QSP manufactures and supplies a complete range of Inflatable Packers throughout North America and Worldwide. Most of our Inflatable Packers contain Inflatable BIMBAR Elements which are reinforced with two layers of steel cables embedded in natural rubber. They are available Standard in Eight different diameters ranging from 1”-2” up to 7”-13”. Complementary to the BIMBAR Standard Packers range, a 9"-15" and an 11”-18” are also offered, which are designed for use in large diameter wells.
The Deflated Packer is lowered into the drilled borehole and then inflated with Inert Gas, Compressor Air or Water via the inflation line. A borehole section is thus isolated and hydrological tests or cement grouting works can be conducted in this area.
Thanks to their modular design, all QSP Packers offer Reliable and Easy Operation. Inflatable Elements can be replaced in the field and Single Packers are easily adapted into Straddle Packers. Our Packers and Accessories are Interchangeable and Field Repairable with other Packers made in the U.S. using BIMBAR or Pétrometalic Glands.
Inflatable Grout PackersA typical grouting job uses either Inflatable or Mechanical Packers. The selection is determined based on the condition of the borehole, the depth of the hole and what support equipment is readily available.
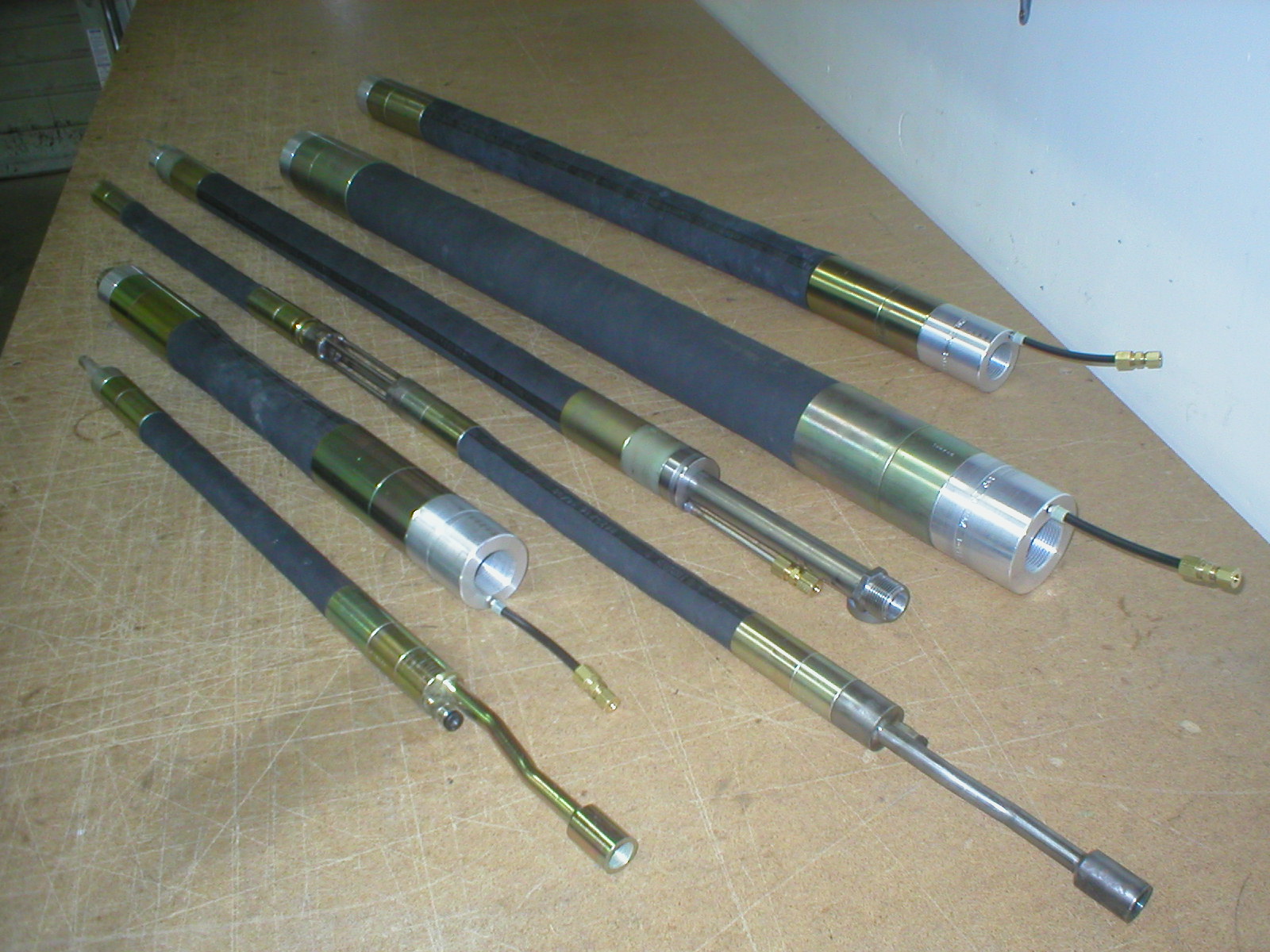
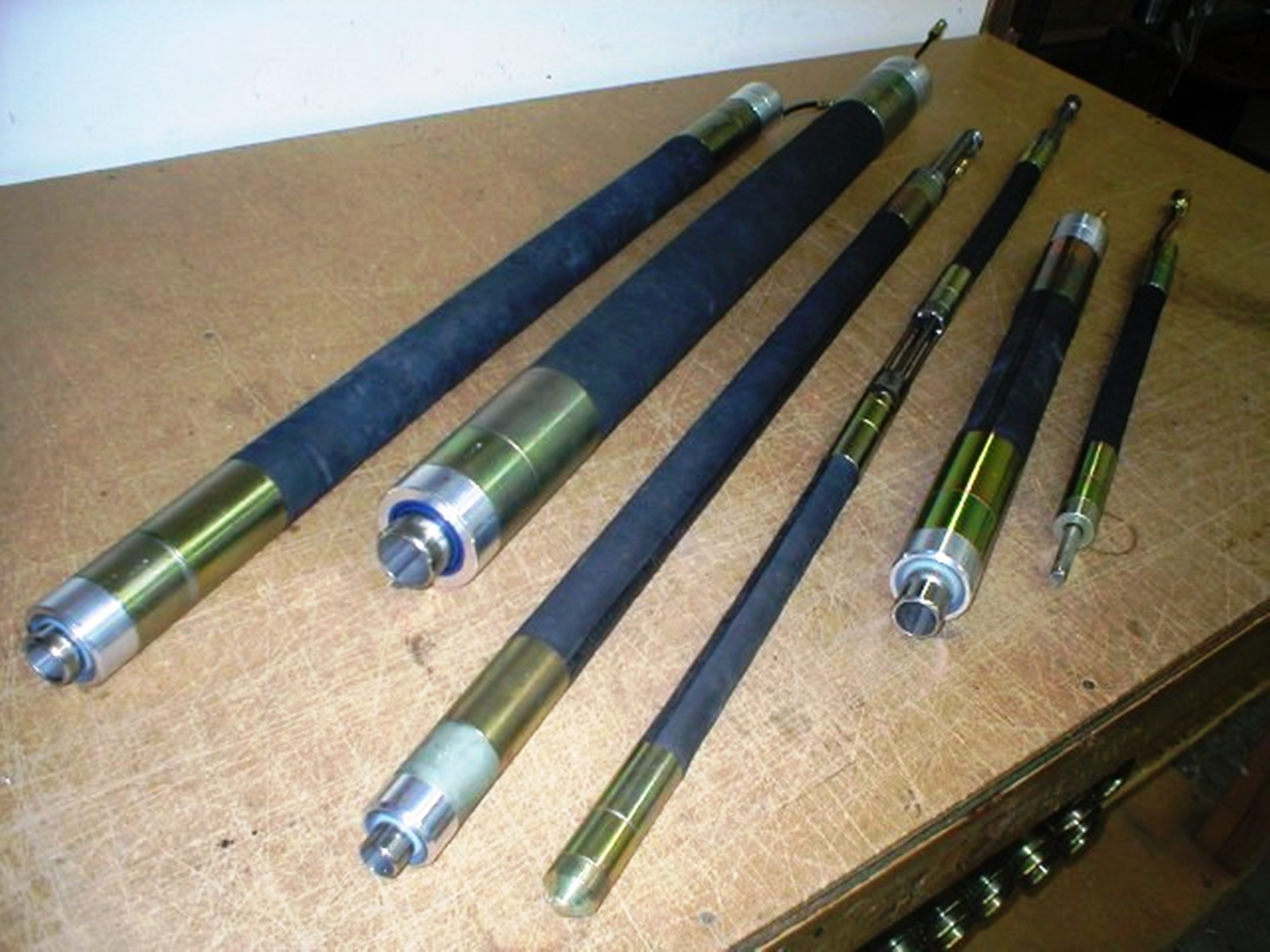
Inflatable Packers range in length from 10” up to five feet or more. They are specifically designed for depths more commonly found in grouting jobs. With their sliding head design, they have the ability to double in size from their run-in diameter and typically furnish a longer seal than that of a Mechanical Packer. The ratio of through-pipe I.D. to packer O.D. is a valuable asset. (Example: 2”-3” O.D. packer is available with a 3/4” I.D. center tube.) QSP’s Grout Packers have integral tube scrapers that remove excess grout that has adhered to the outside of the center tube. The scrapers work each time the packer is deflated.
Mechanical packers work well for surface plugging applications or surface setting for low pressure grouting, and is not going to be injected to any depth, typically only from two to ten feet maximum. They work well in cased holes, but in an irregular borehole, it may not expand adequately for proper sealing of washed-out zones.
Since most grouting projects are in formations that are unstable or open boreholes, Packers using steel reinforced glands can be advantageous. Their excellent memory returning to their at-rest diameter, maximizes their reuse potential by avoiding the common sticking and retrieval problems.
Please give us a call to discuss which packer type best suits your particular project.

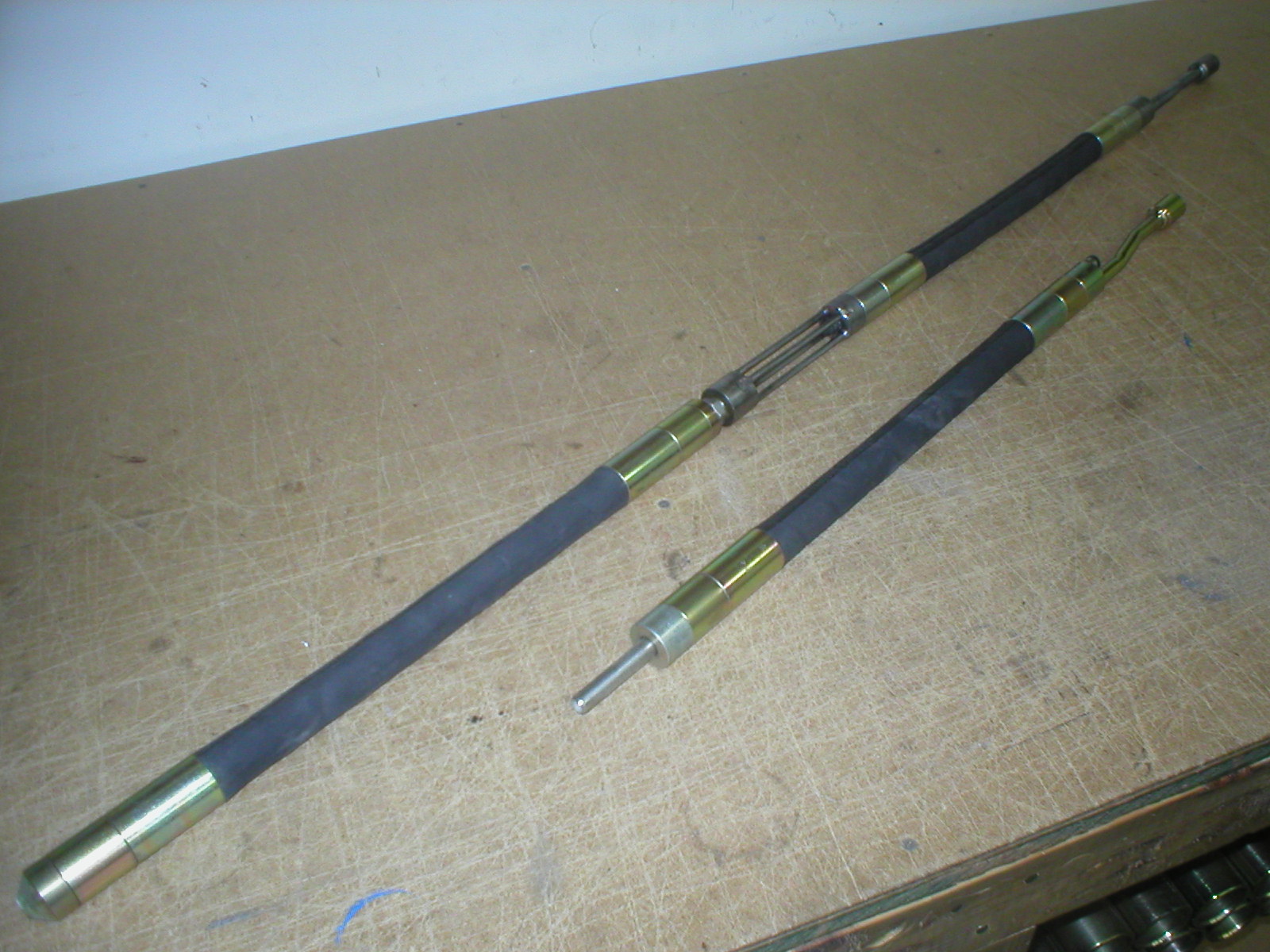
The Wireline System is a timesaving method for conducting permeability testing during core drilling.


The test is carried out with the drill string in place, reducing the time required to test in open or unstable formations. Available for all makes of Wireline Core Barrels (NQ, HQ, and PQ)* Wireline Packers are easily repaired in the field in just minutes.
The Wireline Packers incorporate a bumper that rests inside the throat of the drill bit.
This positions both packers and protects the drill bit. A compression cap on the Seal Tee Assembly prevents pressure loss around the Composite Cable during testing. The Composite Cable itself is composed with a High Pressure 3/16" nylon tube for inflation and a 3/32" steel cable to lower and retrieve the Wireline Packer.
For testing specific zones, a Zone Packer can be easily attached to the lower end of the Wireline Packer.
The Wireline Packer is inverted and the Zone Packer is connected using a perforated tube the length of the required test zone. An inflation tube connects the Wireline Packer and Zone Packer for simultaneous inflation.
* QSP Packers is proud to supply Boart Longyear Company and many other customers Worldwide with Quality Wireline Packers and Accessories that are Compatible to their Wireline/Core Drilling Equipment. Q™ is a Federally Registered Trademark of Boart Longyear Company
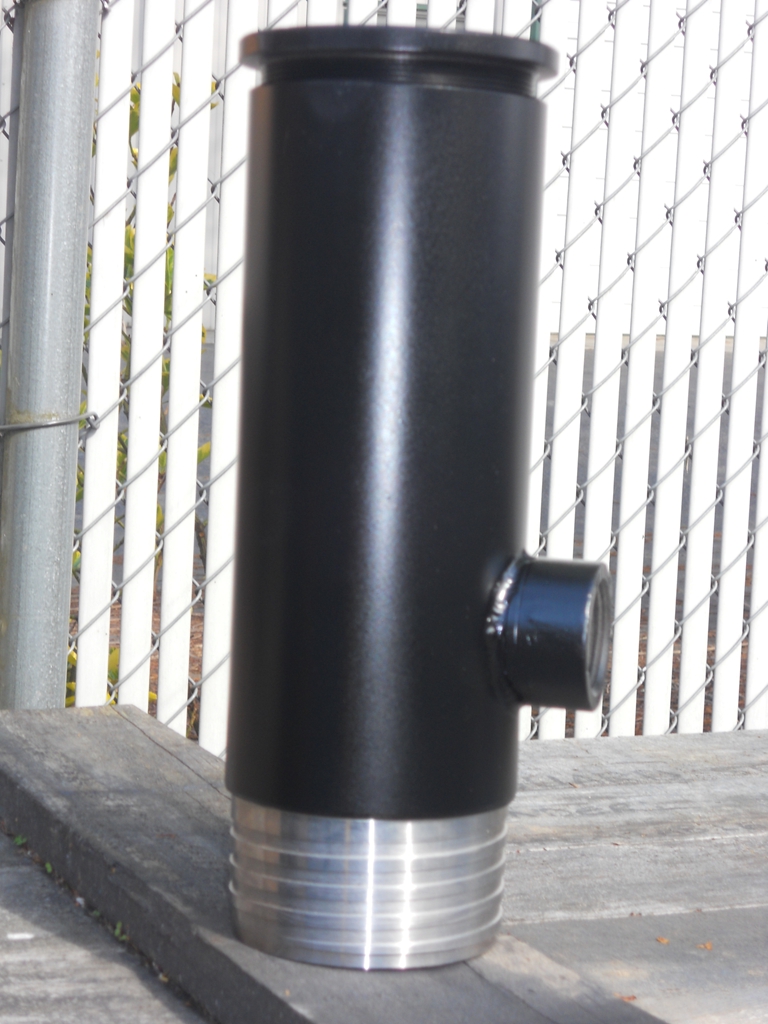
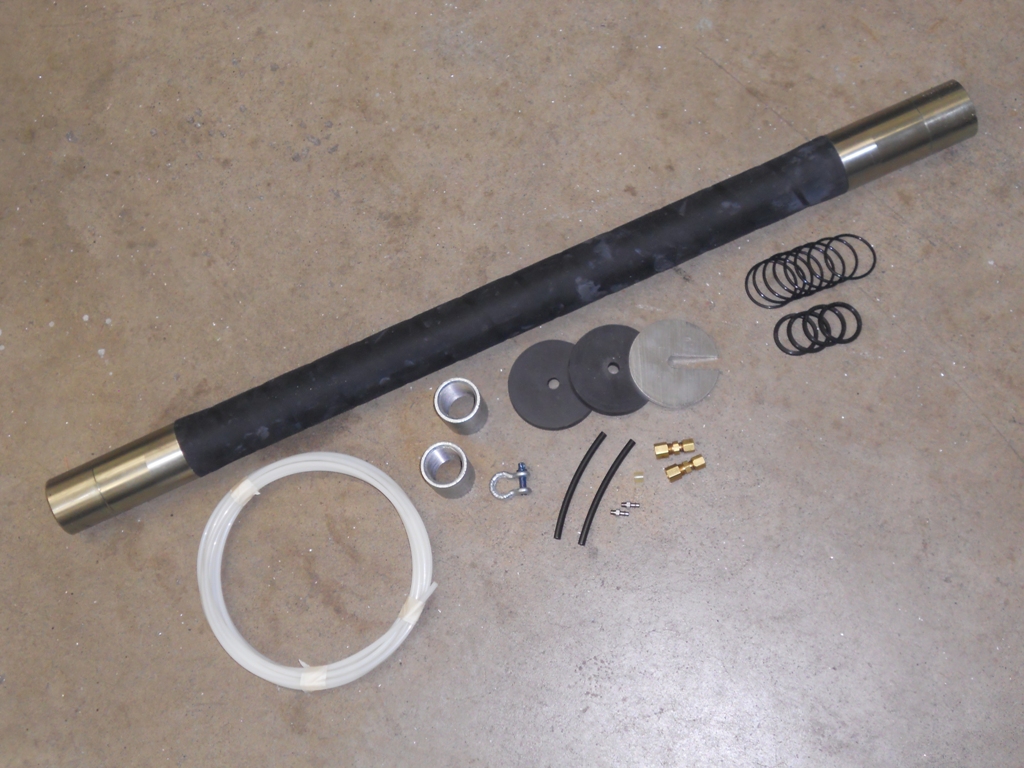
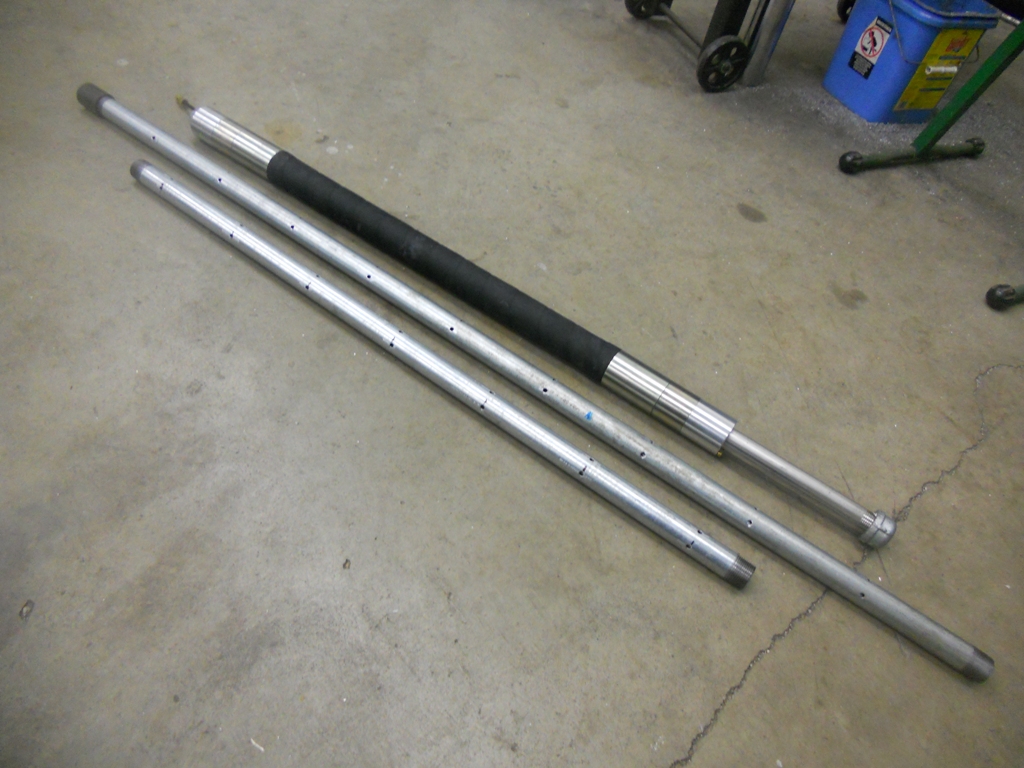
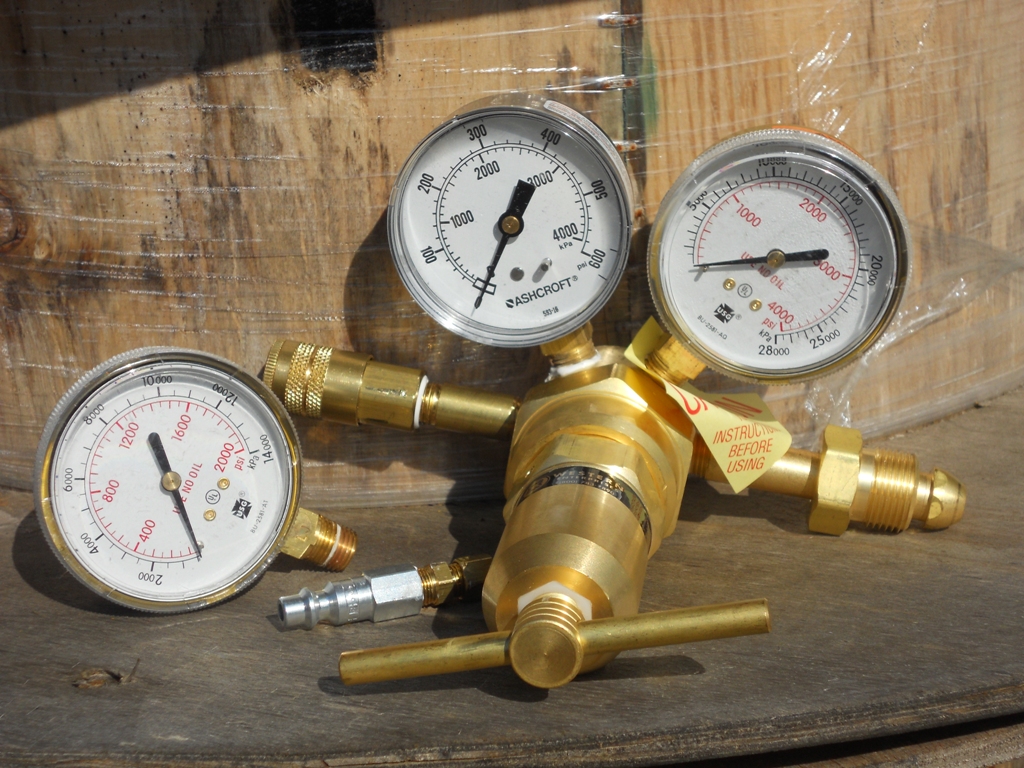
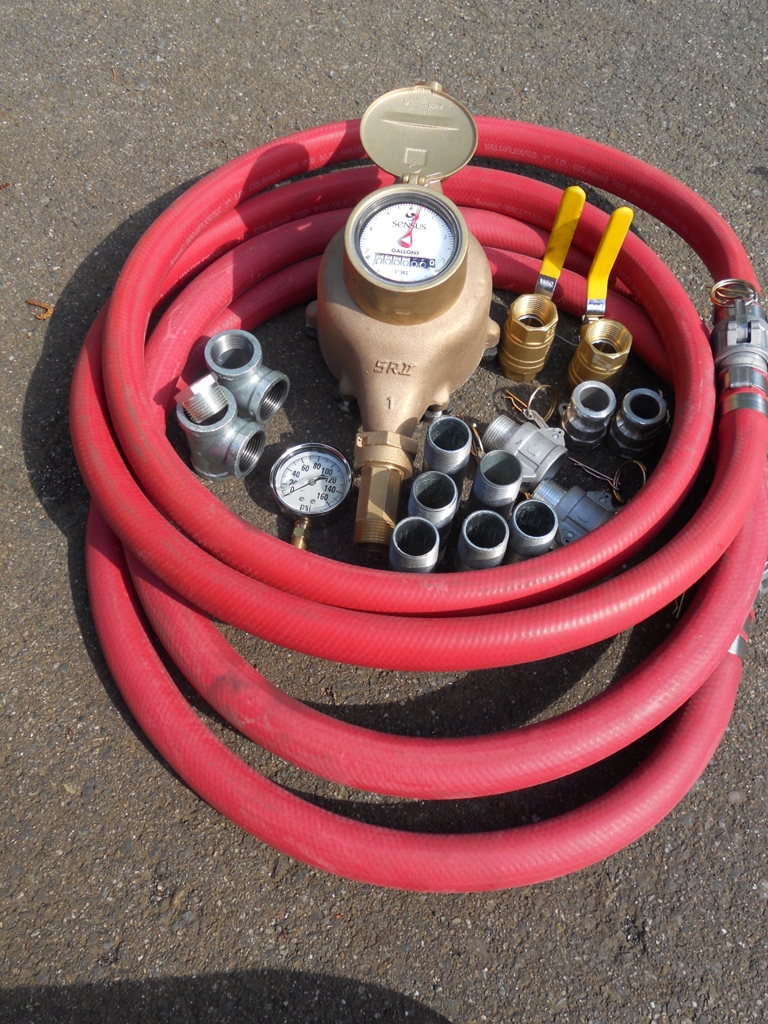
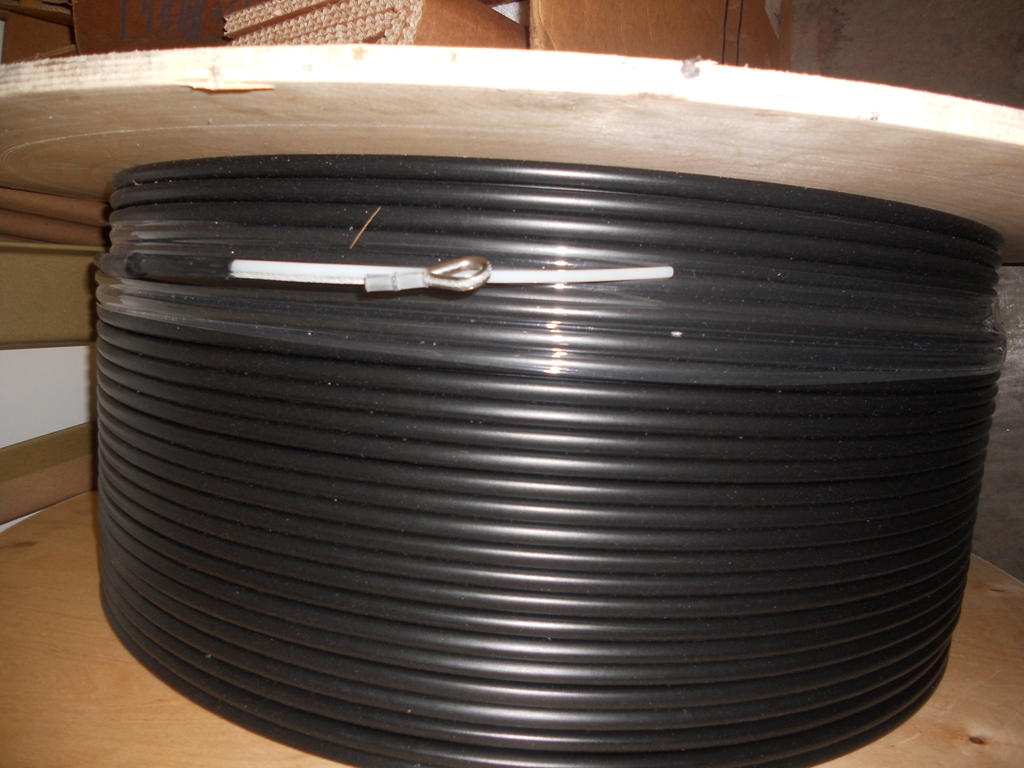

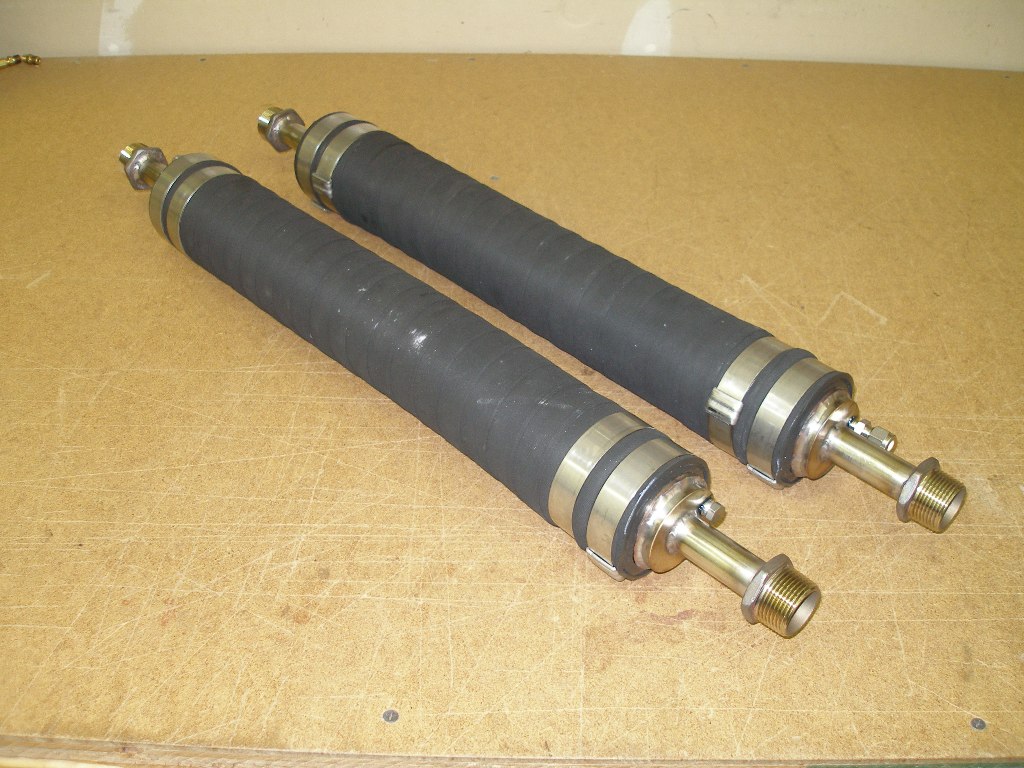
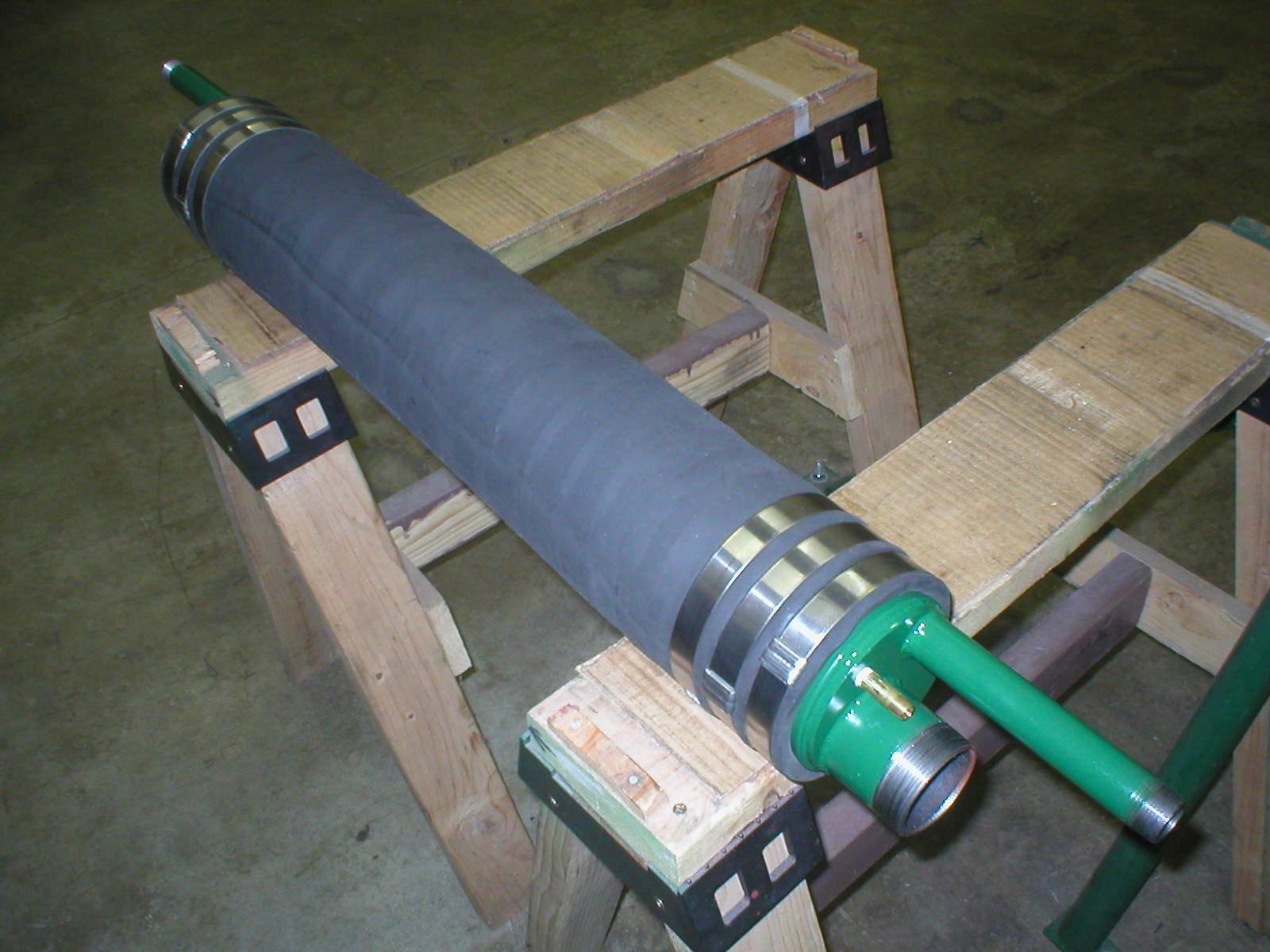
The Environmental Packer is a Fixed-End Style Packer manufactured using either Neoprene, EPDM or Viton® rubber gland element and Type 304 or Type 316 stainless steel. It is designed for applications such as Groundwater Monitoring, Methane gas control or collection (typical in landfills and mines), Vacuum sampling at or below Leachate pads, Formation pressure monitoring, and Vados zone sampling and injection.
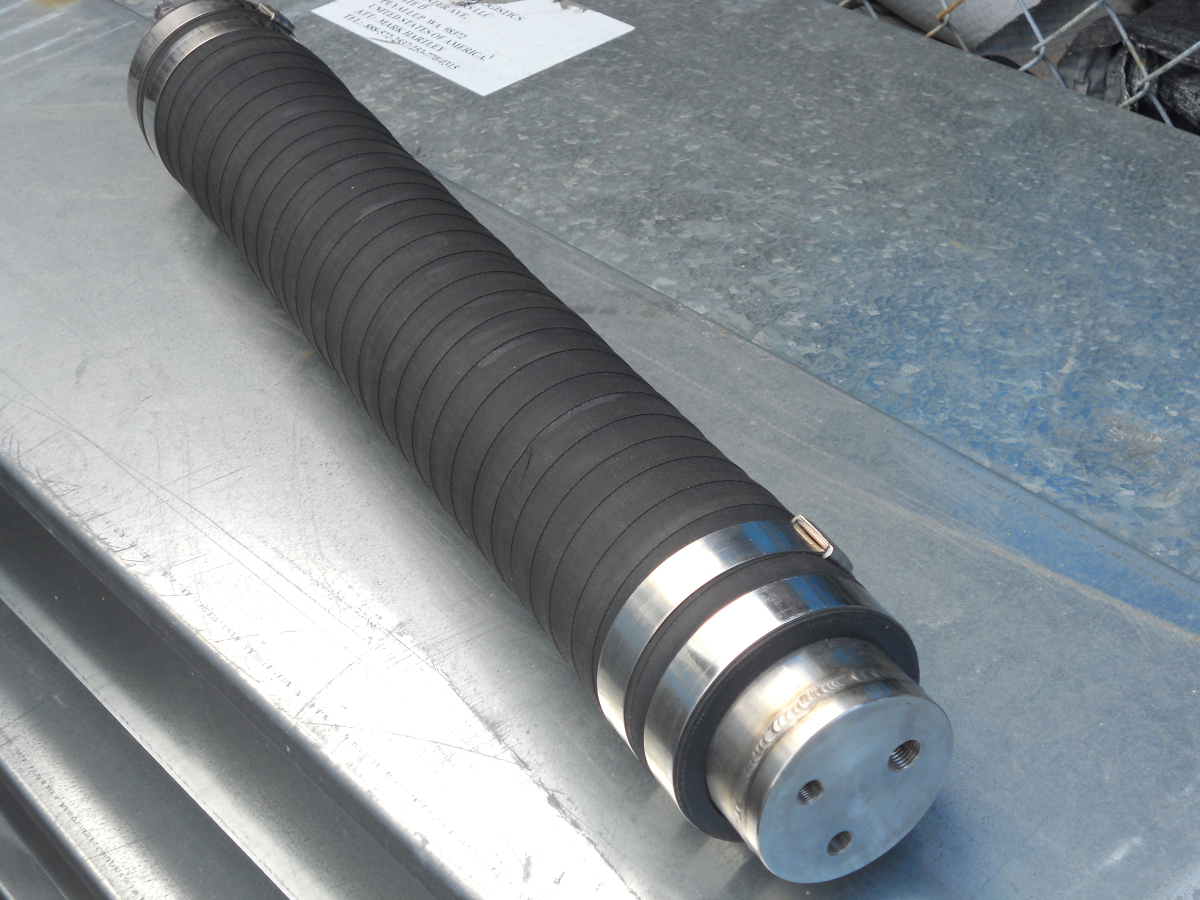
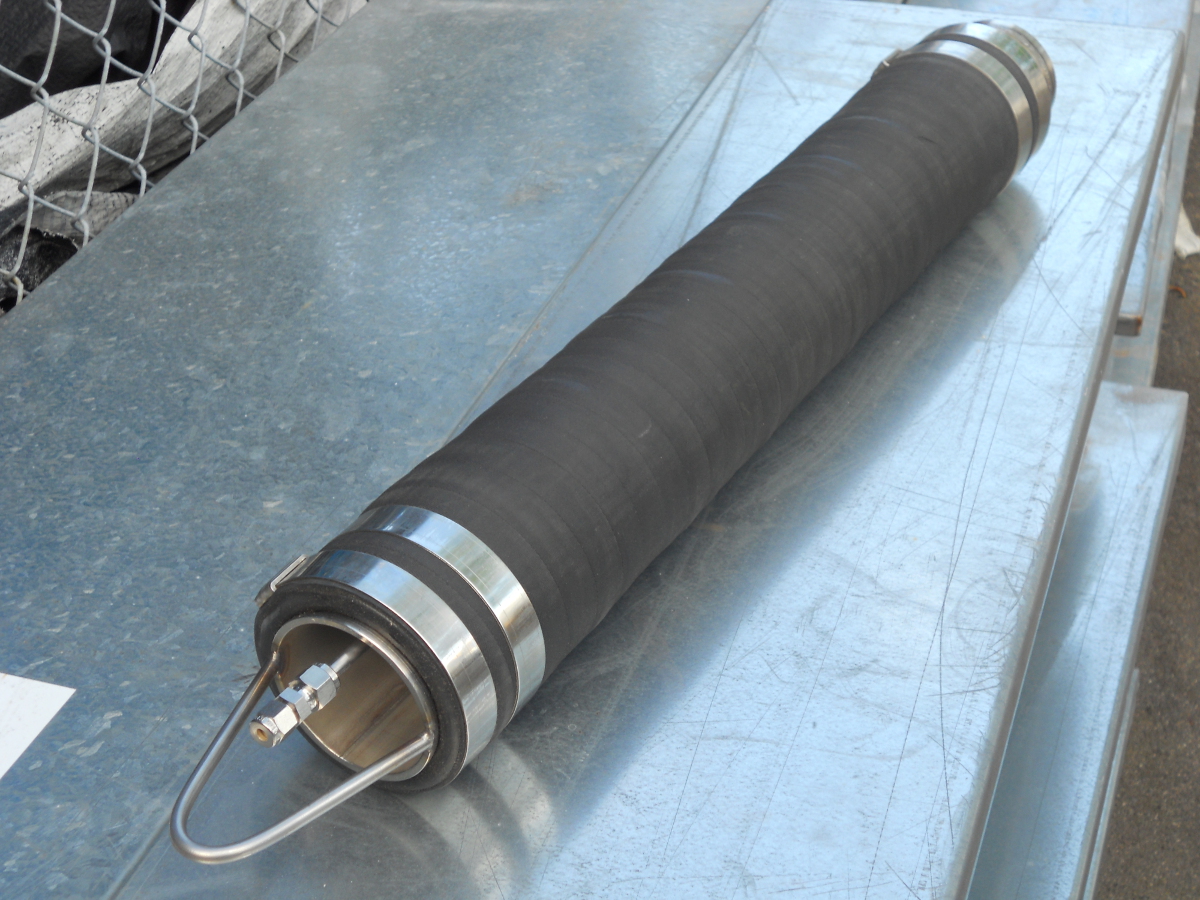
It is designed for use in cased wells* only, and may be used residing above or below the applicable pump (either Bladder, Electric or Piston Sampling Pumps) to significantly reduce purge time and volume. They are available for two inch or larger casing, and if isolating a specific test zone in a well is necessary, two or more Environmental Packers can be adapted to work with the sampling pump. It can be inflated with either inert gas or water. We can custom design systems to fit your specific site requirements. Please call for details.
 Large S.S. and EPDM.jpg)
 Large S.S. and EPDM.jpg)
INSTRUCTIONS TO SET THE PACKER:
* WARNING: Never inflate this packer unless it is confined in a
cased well. Maximum internal pressure must not exceed 200 psi.
1. Lower Packer into the well and inflate (with either inert gas or water) to the static head above
the packer (distance from the packer to the water level x .43).
2. Inflate to 25 psi. This
pressure will expand the gland to the well size.
3. Inflate to 20% of the maximum possible
differential across the Packer. Be sure to use an accurate pressure gauge.
Example: The Packer is set at 100 feet and the water level is at the top of the well. If you withdraw all the water below the Packer, the differential would be 43 psi. In step 3, you would add 9 psi.
Inflatable Packer OptionsQSP designs all of their Packers modularly and the majority of packers are purchased for use as a Single Packer. Monitoring equipment such as Pressure Transducers, Thermistors, Conductivity Probes, pH Probes, or injections ports are common uses with perforated pipe for injection testing. Testing equipment can include Bladder Pumps, Electric or Piston Pumps for pump out testing at various depths and with the ability to isolate various zones.

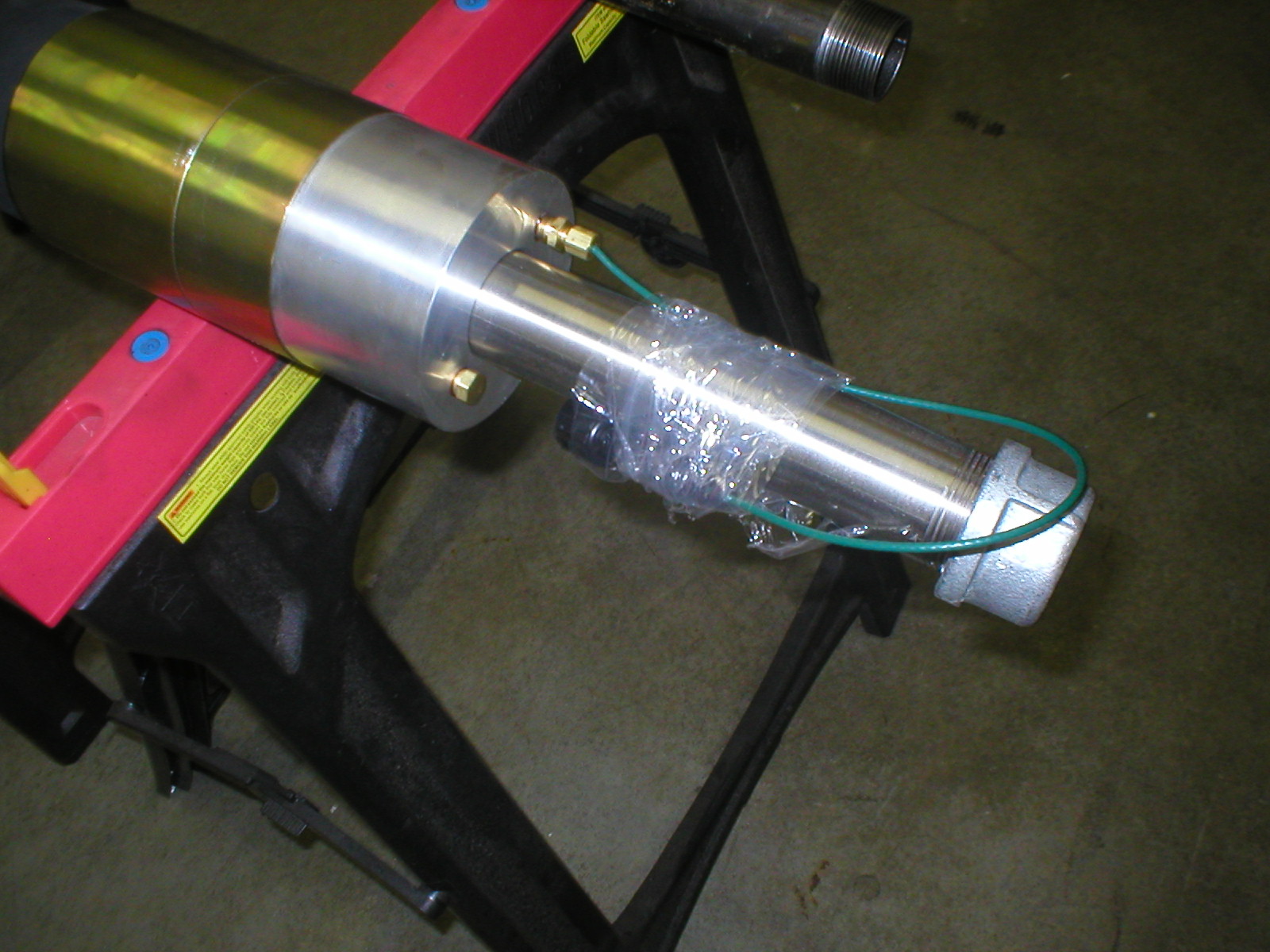
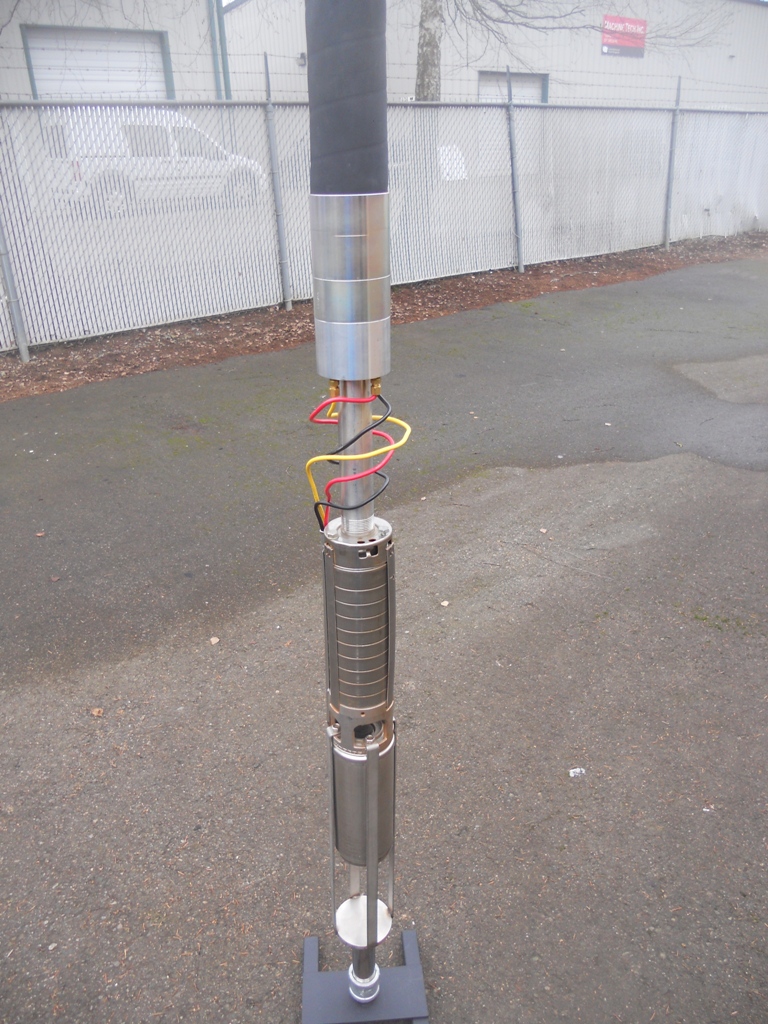


Depending on application or need, these may be designed to work with a Single Packer, residing above or below, but they can also be adapted to reside between two packers in a Straddle System which is the most effective way of isolating a zone for testing. Two or more packers may also be utilized together in a multiple packer system to further isolate zones for testing.
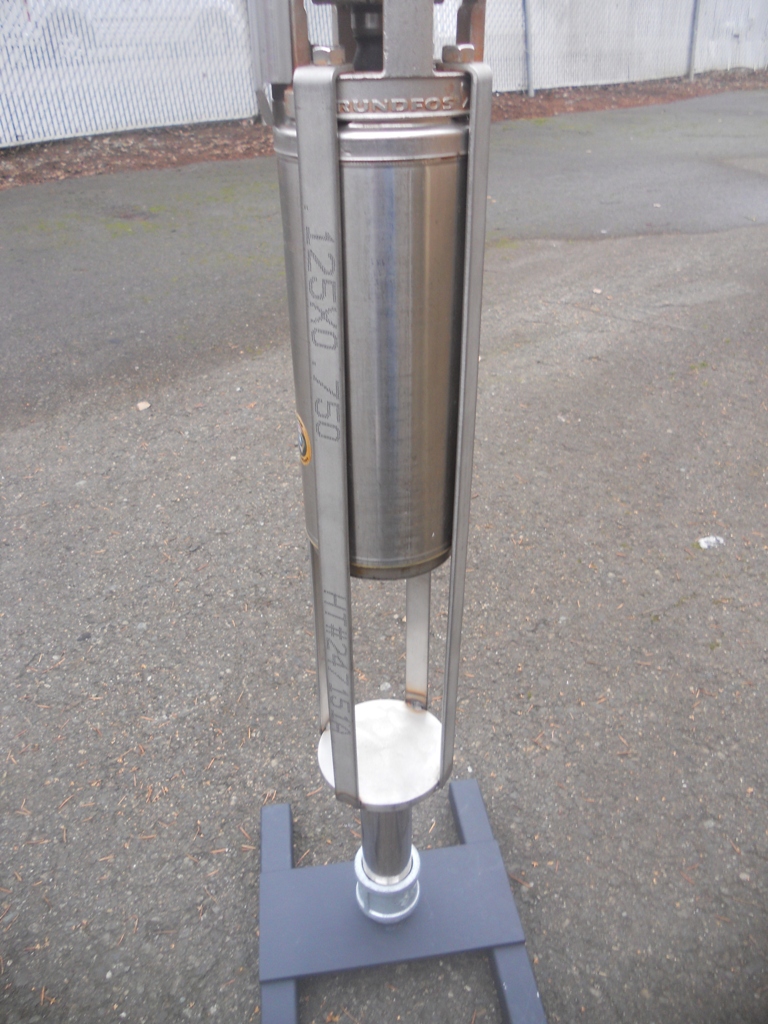
 Head with Feed Thru Options.jpg)
Feed-throughs can be built directly into the head, or if appropriate, in-line adaptors can be incorporated into the system to fit your design needs.
Another advantage of being modular in nature is the ability to offer spare parts for ease of service in the field and cost effective repair, (rather than replacement of an entire system) in many cases.
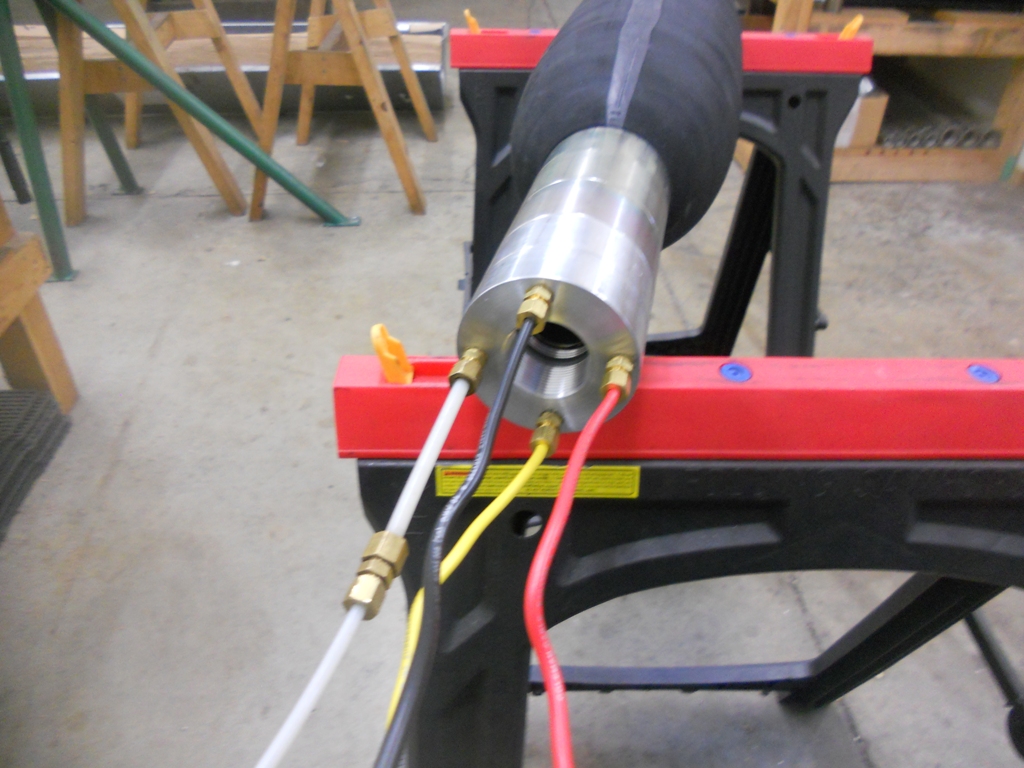
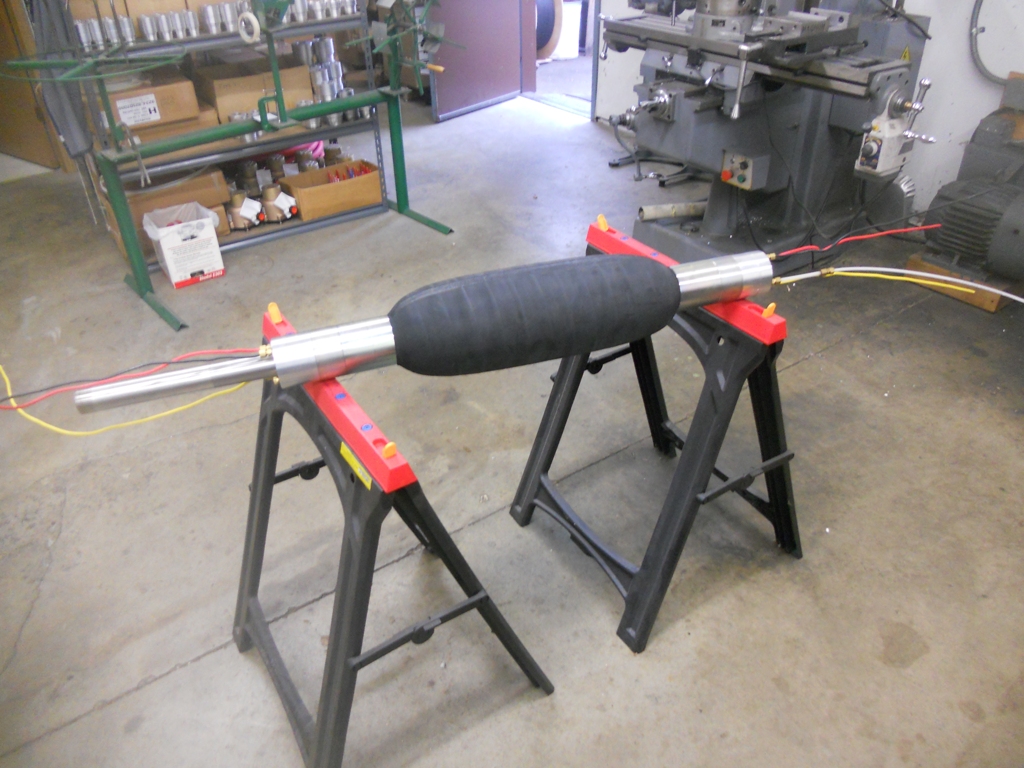
►Water Test Kit
►0-1500 PSI, 0-800 PSI, & 0-400 PSI Regulators with Quick Disconnect fittings
►3/16” & 1/4” High Pressure Nylon
Tubing
►Perforated Tubes for Zone Kits
►Misc. Brass & Steel fittings
►Composite Cable repair kit
►Inflation Tube Jumpers, and Installation Tool
►O-rings and
Seals
All Packer replacement parts can be purchased separately, ie.
Center Tubes
Fixed
Heads
Sliding Heads
Glands
.jpg)
.jpg)
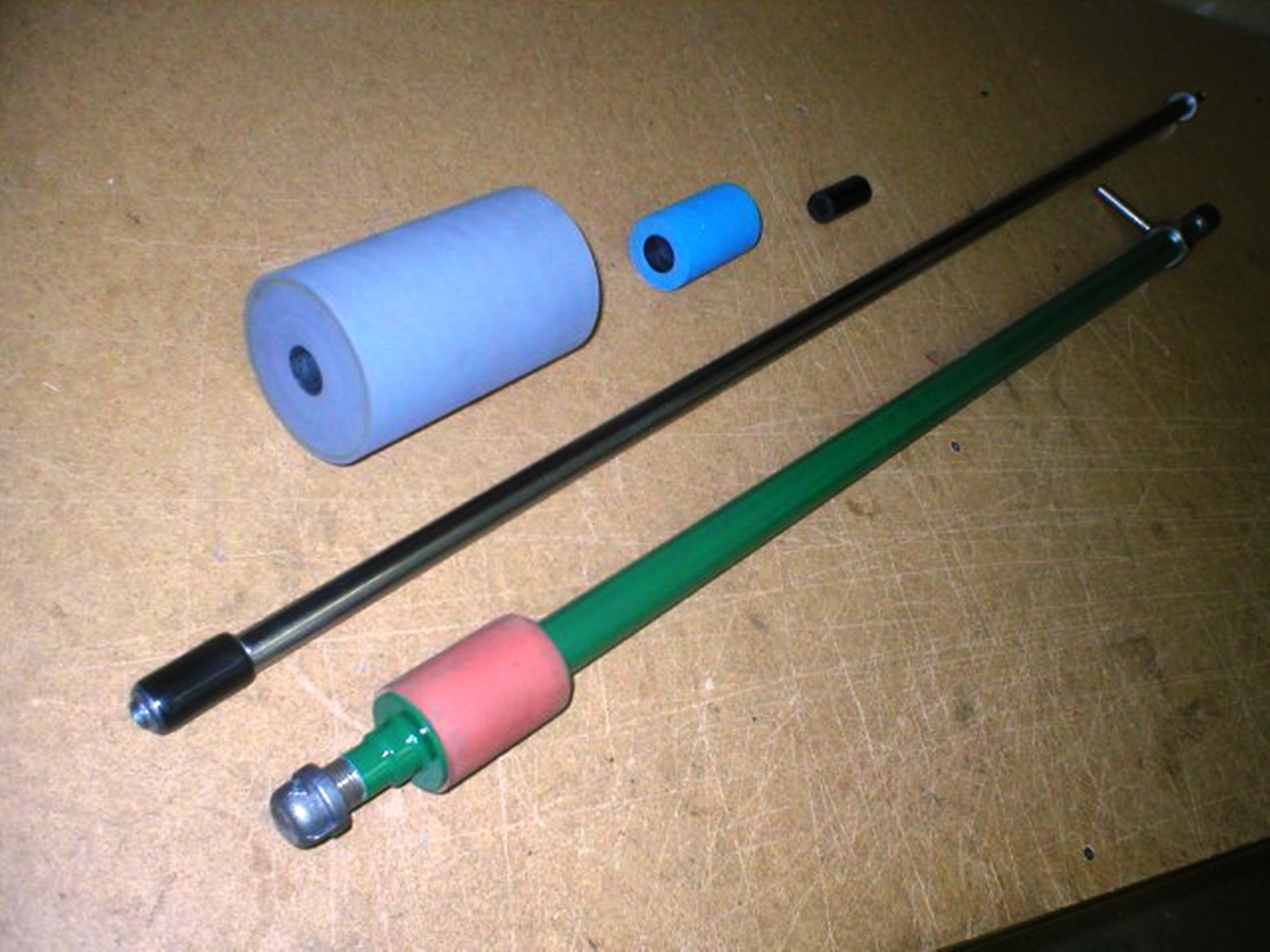
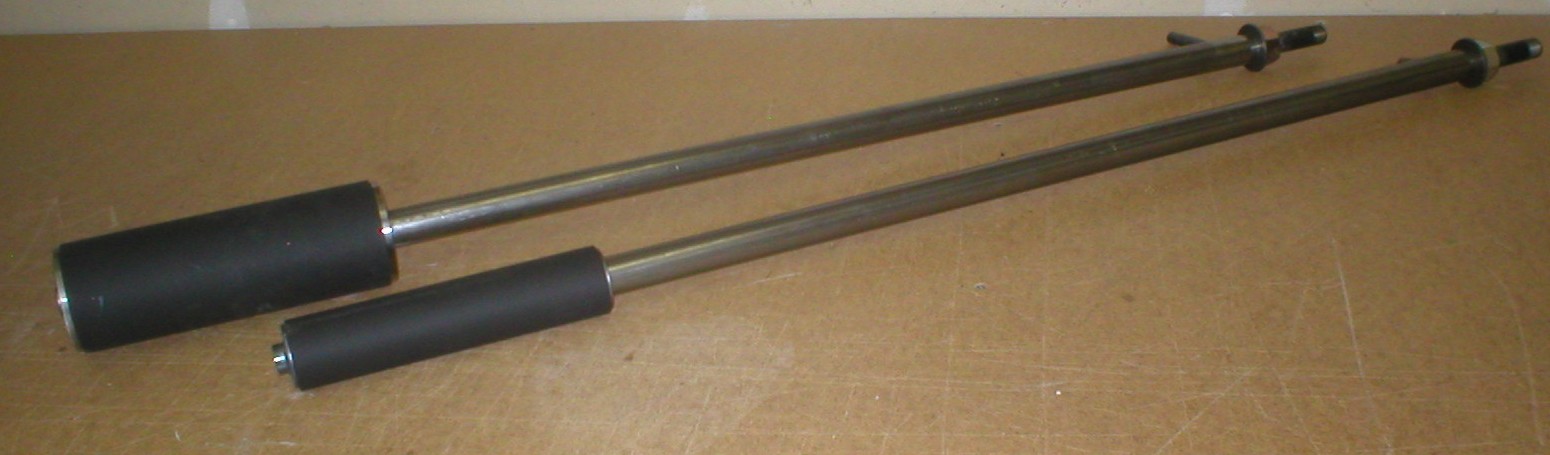
Mechanical Packers sometimes called Surface Set Packers, are a low cost, low pressure, hand set
Packer for Cased Wells, or Smooth Hard Rock Bored Holes. They are made to be set at 12” depth
to 20’ depth. The length is decided by where seal is going to be down hole. They have a
limited expansion range, that is why they are not recommended to be used in Open Holes. Mechanical
Packers are operated by tightening a nut on the surface and forcing two pipes to work against each
other, which compresses the rubber gland to form a seal. Mechanical Packers are used for Freeze
Plugs, Low Pressure Injection, Grouting, Air Sparging, and to control flows out of Artesian Wells.
You can adapt Gages, Valves etc. to meet your needs. Made of S.S. & Neoprene Rubber, or if not a
factor, can be made with standard pipe. Made to fit the I.D. of the Casing size you are using.
Example, 1.85” O.D. to fit in 2” Sch.40 I.D. casing, 3.75” O.D. for 4”
Sch.40 I.D. casing.
Give us a call to discuss your needs.
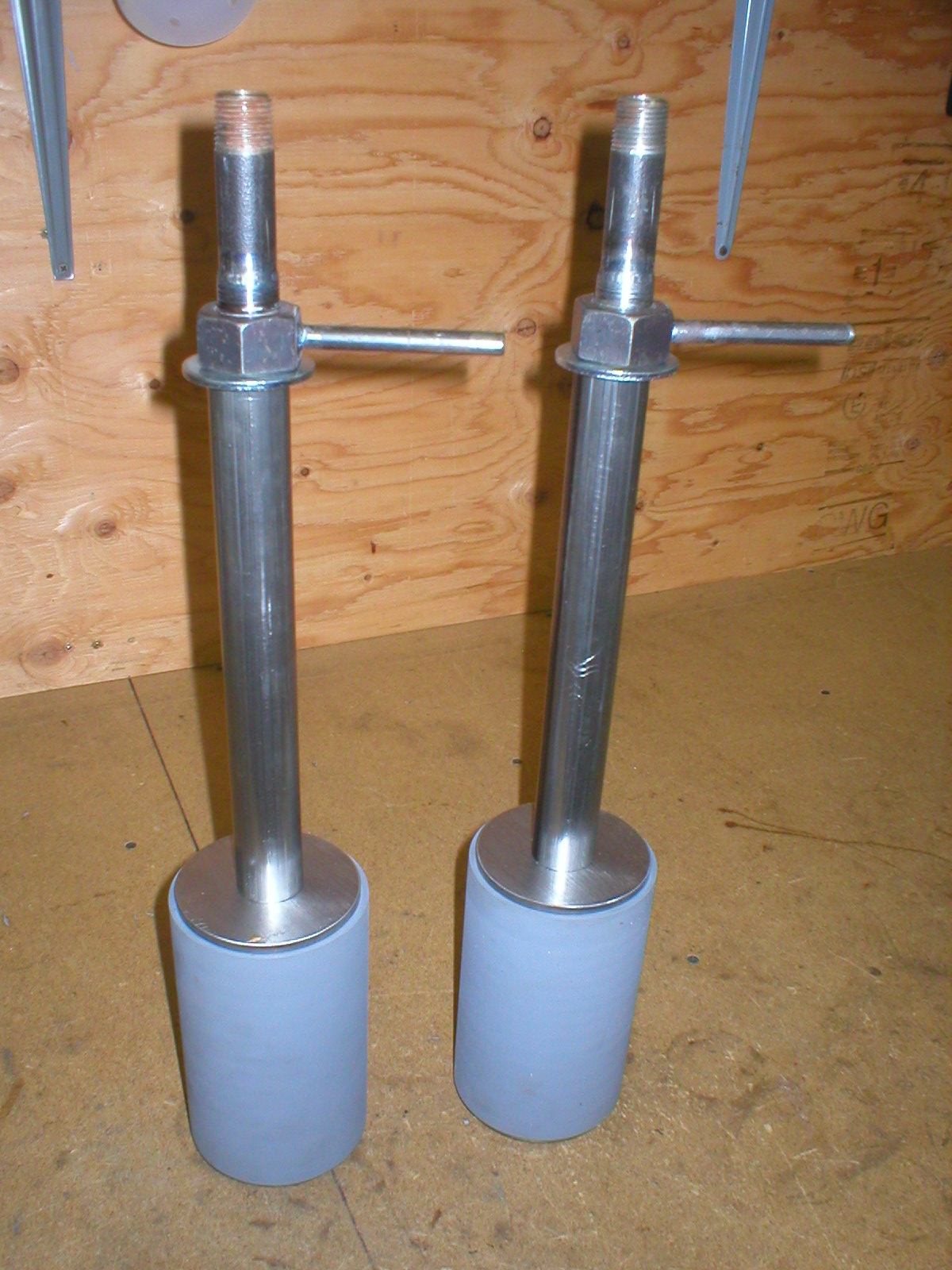
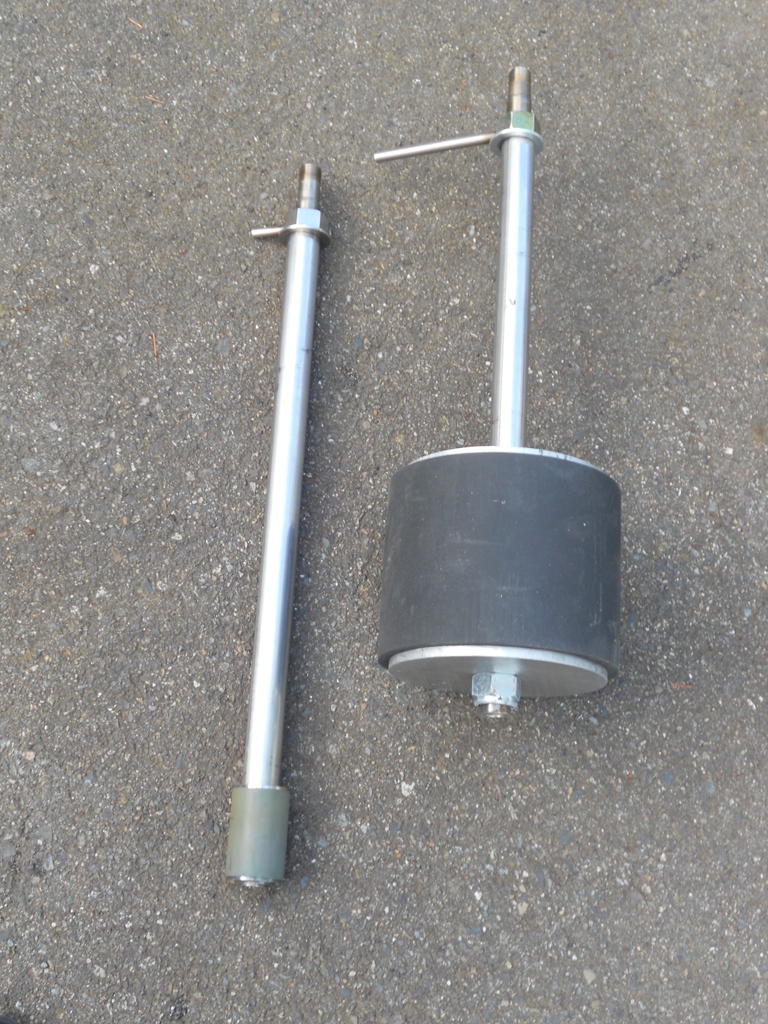